A few months back I got a package in the mail. A fellow woodworker sent me three nice hunks of gorgeous quartersawn chocolate brown oak. I originally wanted to use it to make a staked coffee table, but this oak was too nice for a project like that.
 |
Freshly re-sawn panel that will hopefully make an 18" x 18" panel. |
The nicest piece of furniture we own that I have made is my cherry Shaker side table.
 |
My Shaker side table in cherry that I made a couple years back. |
I used an inordinate amount of lumber for that side table because I tried to choose the best parts of the wood I had in the perfect orientation for that piece. It paid off big time. The above picture looks a bit off, because the base sat a long time before I finished the top and drawer. When it was done, those parts were much lighter in color than the rest. Over time, the whole thing has darkened up nicely, and looks more beautiful every day. Unfortunately I have no picture of it in this state.
The biggest lesson I took from that build was that wasting all that lumber was no waste at all. Grain orientatioin and the thought put in to what grain goes where made all the difference.
Having these beautiful oak boards, all about 1 3/4" thick, is plenty of lumber for this table, as long as I can squeeze everything out of these parts. Since this is all gorgeous quarter sawn wood, I think that it will work.
I spent some time deciding which boards are going to yield which parts. I had briefly thought of resawing the widest piece, to get a panel about 11 inches in which I would take the center of a three piece lamination to make an 18" wide panel for the top. I eventually decided against that, because that wide piece has the straightest grain and will make the best leg stock for the table. The narrowest piece will yield two nice resawn pieces wide enough to get the 18" square top. The grain on this piece had the most pronounced curvature to the grain of the three, so I chose to mark out and crosscut the piece where the curvature makes the least impact. I haven't decided yet if I'll glue those two boards up to be bookmatched or one next to the other. It all depends on what the final look will be like.
The apron boards and the drawer front will come from the third piece that hasn't been mentioned yet. Resawing that board will yield four nice boards for that purpose.
 |
I've started by crosscutting one piece in order to get the length to size before resawing. |
All this resawing is the purpose behind my recent purchase of the giant Dick saw. It is the Ryoba that is 300 mm long, has a much thicker sawplate and larger, more aggressive teeth. It should work well for this.
The reason I bought it is I couldn't get my Diston D-8 that I usually use for resawing in my suitcase, and I didn't want to build a framesaw for the purpose before starting this project. The saw was about 40 Euros from Dictum.
 |
My set up for kerfing my wood before resawing. |
I have been thinking a lot about a kerfing plane. I think getting a good kerf all around a piece of thick wood is a great trick for keeping everything aligned for resawing. I thought that perhaps instead of using a kerfing plane, which I didn't have, I could clamp my Dick saw an appropriate distance off of my bench and run the wood past it.
 |
After some experimentation, I discovered kerfing with the crosscut teeth worked better. |
With the blade removed from the handle and clamped firmly in place, I just pushed the wood past the blade until there was a kerf around 1/4" deep or so all around the piece.
 |
Pull the wood past the clamped blade. |
 |
It seems to work really well! |
Once that was done (and I think with some practice it could be done freehand), it just took some creativity to clamp the piece to my sawbenches (my only work bench surface) in order to saw away.
 |
Deepening the groove on the end grain. |
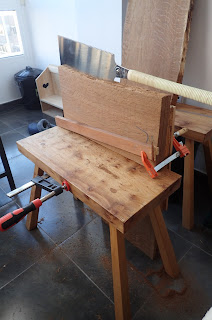 |
Deepening the groove on the long grain. |
With the kerf cut, it is just a matter of sinking the saw in the kerf and connecting the lines. Yes, it sucked, but it was much quicker than waiting until I befriended someone in town with an appropriate bandsaw setup.
 |
The giant Dick saw actually seems to cut fairly efficiently. |
Once I started making progress, I wedged the cut parts open with my shop knife.
 |
For scale, the wood is a bit over nine inches wide. |
I thought I might have to spend a couple days resawing this wide piece, but it was actually finished in a relatively short time. This was the hardest cut of the whole project, so it will be downhill from here.
 |
All the way through! |
As you can see from the first picture in this post, the cut turned out exceptionally well, in my opinion. I think this was the smoothest resaw cut of a wide board I have ever done. The thicker plate on this saw did a nice job of keeping the cut straight. No humps or crazy saw marks!
 |
That's enough work for me for today. |
I clamped the pieces up just in case the inside of the board was a different moisture content than the outside. If it is, it could cup as it dries. However, I'm not too worried as I think the wood has been well dried, and it is quartersawn, which should resist cupping.
Over all, I would have to give this giant Dick saw a positive review. It might not be my first choice for resawing a nine inch wide board, but in my circumstances it worked perfectly. I recommend it if you find yourself in a similar situation.
Next up, resawing the aprons and ripping the legs!