Another day or two, and I wouldn't have finished this chair in June!
 |
Chair is done. |
All kidding aside, I'm glad I took the extra time to do this chair properly. Although it isn't perfect, I am very pleased with the shape and I learned a lot. Mostly thanks to Peter Galberts' book.
Here are a few pics of the last part of the build. The first is of the wedged leg from the top of the seat. I wound up reaming the holes quite a bit larger than the 5/8" which is usual. I did this because I felt it made for a stronger joint, which I think was necessary due to the extreme splay and rake of the legs.
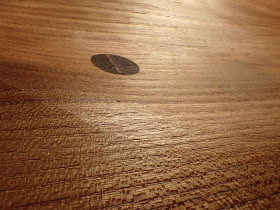 |
Fumed oak leg with an elm wedge in the elm seat. |
There is a little spring to this chair. The legs tend to splay a little more when you put your weight in it, but it feels solid to the sitter. The back springs a little, too. I'll let you know if anything ever breaks.
 |
Small chamfer on the feet. |
I used a block plane to chamfer the feet. This chair will live on a wooden floor, so the intent is to put some felt protectors on the feet to avoid scratching anything. I have only ever had good luck with the felt protectors that you nail in. The sticky-tape ones tend to come off over time, and the next set doesn't stick as well as the last.
Here is a pic of the chair while dry-fitting the back. This was the first time I got to see the whole chair together in one piece. All that was left from this point was to figure out how to permanently attach it. I decided to wedge everything.
 |
Dry fit of the back. |
Here is how I did the blind wedges: I cut some wedge stock from some scrap mahogany I had laying around (it was the right width). I sawed a kerf in the end of the stick a little less than the depth of the mortise. I placed the wedge loosely in the kerf with glue on one side, slopped glue around the end of the stick that will enter the mortise, and beat the crap out of it with a mallet.
 |
Shortly before being driven into the mortise. I did actually trim this wedge a little shorter right after this photo. |
The idea is the wedge will force the ends of the stick in the mortise apart a bit making the joint tighter the farther it is driven in.
 |
Imagine glue everywhere. |
This went relatively smoothly. To drive the sticks, I didn't clamp it in my face vice, I clamped the crest upside down on my bench to my planing stop.
 |
Driven home. |
For the bottom, I used through mortises and was able to drive wedges after the sticks were in place. Once I did this, I flush cut them so they wouldn't be visible when looking at the chair.
 |
Through mortises for the sticks in the seat. |
And that's it! This chair really wouldn't take too long to make if one was able to spend a few days uninterrupted. The reason for me was I had not much time to do woodworking during this project, I had breaks of a week or so between shop sessions. Even so, this project didn't really take THAT long. I recommend a chair in this style to any aspiring chair maker.
 |
The finished chair. |
I'll soon post some more glamour shots of the chair, along with some of the more technical aspects of it and the build.
Hi Brian,
ReplyDeletenice build. Came out great.
I've got two questions. 1) are the legs directly inserted into the seat plank or did you have used battens on the underside?
2) How do you set the angles for splay and rake? Have you eyeballed it, or did you take the measurements from the mentioned book?
Cheers,
Stefan
Hi Stefan,
DeleteGood questions! Thanks for the compliment.
Yes, the legs pierce the seat blank. It doesn't look like it, but this elm blank is more than two inches thick. It should be plenty strong for this chair, as elm doesn't split easily. This is traditional chair joinery, and Welsh stick chairs were often made from single elm blanks just like this.
As far as the rake and splay, I went super radical with 25 degrees splay and 25 rake on the back legs. There is no magic to those numbers, I just liked the way some of the old stick chairs with radical splay look. I think not too many people build them that way anymore, as it probably creates a bit more stress on the seat blank than other, more upright angles.
The easiest way to drill these is to find the sightline for your planned angles using Peter Galbert's angle finder from his book.
Brian,
ReplyDeleteit looks awesome! Well done!
Thanks, Michael!
DeleteHi Brian
ReplyDeleteThat looks absolutely stunning, well done. I really like the splay and rake of the legs, it is super cool.
Cheers
Gerhard
Thanks Gerhard! I really appreciate it.
DeleteThe splay of the legs seems a bit extreme to my eye, but as long as they don't break, all is good :-)
ReplyDeleteNo matter my tastes, I applaud your decisions, it IS a nice looking chair.
It is by experimenting that we grow...
Bob, who added a chair on his to do list :-)
Hey Bob! Adding a chair to your list makes me happy. More woodworkers should do it. I should have done it long ago. There is no reason to fear building a chair. The worst that can happen is it falls apart and you learn something.
DeleteThe leg splay is indeed extreme, but there are historical examples of this. Just google "Welsch Stick Chair," and look at the photos that pop up.
The biggest negative about this splay, is it makes the chair legs really far apart. I don't think it would be practical to have a bunch of these around a dining table, the legs would continually get tangled up with each other. If I do this again, I would probably put the legs a bit closer together on the seat blank.
i love the aggressive splay! it evokes for me the image of a cat fixin' to pounce!
ReplyDeleteI also like the graceful way you taper the edges of the seat. This is an inspiring project, i think i need to make one now!
-Adam of Oakland, CA
Hi Adam, thanks for the compliment! send some pictures when you do, I would love to see it.
DeleteAs Brian's official "chair-tester" and I would like to write how comfortable that seat is! In Germany so many chairs are covered with a cushion for comfort - but this one is carved like a saddle and feels just right. I don't know how he did it, but he did! Well done. John
ReplyDeleteThanks, John!
DeleteBravo Brian! The chair is beautiful! With the radical rake and splay I am not surprised that you get some spring when sitting. I am most curious about the blind wedges. I have often thought about using them in a chair but just as quickly discarded the idea. Not now, I must give it a go. Thanks for the inspiration.
ReplyDeleteI should finish my chair this month, if life doesn't get in the way anymore than it has. It was a June start with an open ended finish, correct?
You better hurry, June is almost over!
DeleteI didn't know I should worry about the blind wedges. I just cut the kerf a little less than the depth of the mortice, cut the wedge so it wasn't longer than the kerf, aligned the wedge so it would spread out toward end grain rather than short grain, and pounded them in until they stopped. It was the best way I could think of for this crest.
You did a great job on this chair, Brian! Looks so nice.
ReplyDeleteThanks, Mom!
Delete